Wednesday, December 29, 2010
Got a Haunch, not a Hunch!
I spent this morning fine tuning the mortise and tenon joints for the sides of the tool chest. The way I work is to use the table saw and mortiser for the beginning stages and then hand tools and quiet work to do the final fitting. Sometimes you luck out on cutting the tenon cheeks but usually you have to pare them down for that perfect fit. Through the years though I've learned that perfection and woodworking rarely go hand in hand. In the past, I've used a chisel or rabbet plane to work on the tenon cheeks and it was okay. Recently I learned of another method:
This is by using a Stanley #71 Router plane. That's right, this is one router you don't have to plug in! This model dates somewhere in the 40's and I really enjoy working with it. The trick was to take a scrap piece of wood that is the same thickness as what you're working on to support both sides of the plane. This method insures that the cheek will be even, sometimes a chisel will cut a slight angle so this gives more control. This also gives a good view of the haunch cut on the end of the tenon. Here's another view of it:
The purpose of a haunch is to prevent the piece from twisting. I created the groove on the inside of these pieces with a dado head on the tablesaw. This is where the Maple panel will float in. You can see how the tenon was notched so that only a small portion of it goes to the top of the piece. It's a pretty common method of making a frame and panel piece. In retrospect, I probably should have made two tenons as they are pretty wide but I think it'll work out fine.
Another thing I realized today is that Alder, although classified as a hardwood, is pretty soft. Trimming with chisels proved that so I'll have to hone them well before starting the dovetails for the drawers. It's funny that a soft wood is harder to cut than a hardwood -- seems kind of backwards! In practice chisel work on softer woods like Alder or Pine is more difficult because the wood fibers will "smush" rather than cut cleanly unless the chisel is extremely sharp. Anxious to see how the Bloodwood works, that's where the half blind dovetail pins come in, the tails will be the Alder and sides of the drawers.
Keep learning and keep your chisel sharp!!
This is by using a Stanley #71 Router plane. That's right, this is one router you don't have to plug in! This model dates somewhere in the 40's and I really enjoy working with it. The trick was to take a scrap piece of wood that is the same thickness as what you're working on to support both sides of the plane. This method insures that the cheek will be even, sometimes a chisel will cut a slight angle so this gives more control. This also gives a good view of the haunch cut on the end of the tenon. Here's another view of it:
The purpose of a haunch is to prevent the piece from twisting. I created the groove on the inside of these pieces with a dado head on the tablesaw. This is where the Maple panel will float in. You can see how the tenon was notched so that only a small portion of it goes to the top of the piece. It's a pretty common method of making a frame and panel piece. In retrospect, I probably should have made two tenons as they are pretty wide but I think it'll work out fine.
Another thing I realized today is that Alder, although classified as a hardwood, is pretty soft. Trimming with chisels proved that so I'll have to hone them well before starting the dovetails for the drawers. It's funny that a soft wood is harder to cut than a hardwood -- seems kind of backwards! In practice chisel work on softer woods like Alder or Pine is more difficult because the wood fibers will "smush" rather than cut cleanly unless the chisel is extremely sharp. Anxious to see how the Bloodwood works, that's where the half blind dovetail pins come in, the tails will be the Alder and sides of the drawers.
Keep learning and keep your chisel sharp!!
Monday, December 27, 2010
Progress on the Tool Chest
As I mentioned in my last blog I'm starting to build a chest for my carving chisels. I do need a safe place to store them as they sometimes fall out of the leather tool rolls I'm currently using. Since the economy has slowed down with paying jobs being scarce, this will keep me in the shop, allow me to utilize odd pieces of material, and most importantly, give me a chance to work on new skills and hone the ones I have.
In many traditionally built pieces the back is made of solid wood, contemporary design has us making backs from plywood where you don't have to worry about contraction and expansion of the wood across the grain with changes in the humidity. I had a short length of 8/4 Maple which I re-sawed and turned into several pieces measuring 3/8" thick and about 3" wide. Here's the pictorial sequence of how I formed tongue and groove joints on these to turn them into my floating panel for the back of the chest.
First step was to clamp a piece of MDF to the table saw, run a rip blade through it and cut a 1/8" groove in the center of one edge of each board. This was cut 1/4" deep. The piece of MDF is there so the piece won't fall into the slot for the blade on the insert -- much safer this way.

Next I set up a 3/8" rabbet bit and cut the opposite side of each board to create the tongue. I used that new fence I mentioned in a previous blog and am happy to report it sucked up about 90% of the sawdust -- nice improvement!
Here are the boards when they're assembled. More than enough to span the panel that will make up the back of the chest.
Although I have made a general sketch of this chest, much of it is being designed "on the fly". If this were a commission I wouldn't have so much leeway. Also, since I'm using leftover lumber that dictates my sizes too. Tomorrow will be spent making the side panels. They will be made out of the only wood I purchased, Alder, and have maple panels.
In many traditionally built pieces the back is made of solid wood, contemporary design has us making backs from plywood where you don't have to worry about contraction and expansion of the wood across the grain with changes in the humidity. I had a short length of 8/4 Maple which I re-sawed and turned into several pieces measuring 3/8" thick and about 3" wide. Here's the pictorial sequence of how I formed tongue and groove joints on these to turn them into my floating panel for the back of the chest.
First step was to clamp a piece of MDF to the table saw, run a rip blade through it and cut a 1/8" groove in the center of one edge of each board. This was cut 1/4" deep. The piece of MDF is there so the piece won't fall into the slot for the blade on the insert -- much safer this way.

Next I set up a 3/8" rabbet bit and cut the opposite side of each board to create the tongue. I used that new fence I mentioned in a previous blog and am happy to report it sucked up about 90% of the sawdust -- nice improvement!
Here are the boards when they're assembled. More than enough to span the panel that will make up the back of the chest.
Although I have made a general sketch of this chest, much of it is being designed "on the fly". If this were a commission I wouldn't have so much leeway. Also, since I'm using leftover lumber that dictates my sizes too. Tomorrow will be spent making the side panels. They will be made out of the only wood I purchased, Alder, and have maple panels.
Wednesday, December 22, 2010
Rainy Las Vegas
Rain and Las Vegas are not found in the same sentence except during our monsoon season but boy, it's been a steady rain for several days. That means that fitting joints can become problematic due to the unusually high humidity. I remember at San Francisco State people would fit a dovetail or tenon in the evening and then if they tried to assemble the next morning the fog/humidity made the wood swell up and no longer fit! You almost had to fit and glue during the same time period. Currently I'm working on making a chest for my carving chisels out of various pieces of wood I have left in the shop. It's also going to be a practice piece where I can improve my dovetail cutting abilities. I know that I could use jigs, routers, tablesaws, etc. to do the joinery but there's just something about doing it the old ways. At this point I'm preparing the stock. The framework will be made of Alder which I had to buy. The drawer fronts and lid will be made of Bloodwood that I had from another project. The materials I have on hand dictated the size of the chest. I also resawed a piece of Cherry which I plan to carve and use for the panel on the lid of this chest. As soon as I get something that's worth photographing I'll share the progress on the blog. Looking forward (with trepidation) to seeing how the Bloodwood will take to half blind dovetails!
In the meantime,here is a shot of the last series of picture frames that are now hung in the dining room:
In the meantime,here is a shot of the last series of picture frames that are now hung in the dining room:
They are the series of threes that Diane is currently working. The upper set is called "Elegance" and she used classic ladies hats, pearls, and gloves of the time. I particularly like the upper left painting that shows a cover shot on a magazine with the ladies eyes peeking out. The lower series is unnamed as of now but maybe "Cafe auLait" would be appropriate -- it's waiting on the center painting to be completed.
From a woodworking point of view I like the way the textures and details show on the wood. The upper series were made of Beech and then dyed, French polished, and waxed. The lower series were made of Poplar, gessoed, textured, and sprayed with a red undercoat followed with a satin oil-bronze finish. Although different the goal was to have the light pick up the textures and details of the frame without drawing attention away from the paintings. I think we succeeded!
Well, time to get out to the shop. It's late enough where the neighbors should be awake and up by now, if not the planer will be their alarm clock.
Thursday, December 9, 2010
New Shop Aide & Frame Progress
One of the things that happen as you pursue this craft is that you learn about methods others have come up with to make life easier. I just found one in Fine Woodworking magazine and decided to see how it worked. For the picture frames I need to cut flutes in the panel with my router mounted in my homemade router table. The biggest hassle here is the fine dust it creates while cutting. Here's a good solution:
This is essentially a hollow box with a hardwood cleat (between fence and box) that has holes in it so that the clamps attach it to the tablesaw fence. I drilled a hole to at the end to attach the shop vacs hose. As we woodworkers tend to do I modified it somewhat by cutting a semi-circle in both the top and bottom pieces for the bit. The purpose is so that I can use this on either side of the fence and still keep the vacuum hose at the rear. Depending on the bit and my feed direction, the auxiliary fence may need to placed on either side of the tablesaw fence. I also added a baffle inside to hep channel the dust into the hose -- worked well, even when cutting all of the flutes on the panel faces!
Things are going nicely on the picture frames. Many, many steps are required to make the 12 sides that are needed to create the 3 frames. I'm making two extra pieces just in case. It's funny how that works, if I make extra parts I never seem to need them but if I don't, then I screw something up -- cheap insurance I guess! Anyway, here's how things are looking now:
The pieces on the left are the panels. Besides cutting to correct size each one needed to have the outer edge shaped and the tongue cut on the opposite edge, this was done on the shaper. Then each needed their 3 flutes cut with the router table that I mentioned above. The pieces on the right will become the sight edge. These had the bead formed on the shaper, a groove for the tongue of the panel, and finally the rabbet was cut for the painting to sit into. Next up is sanding the flutes, planing the faces and then gluing them together as shown in the middle. Let's see, miter, biscuit, glue, clamp, dye, shellac ......... hmm, should be done in a week or two.
This is essentially a hollow box with a hardwood cleat (between fence and box) that has holes in it so that the clamps attach it to the tablesaw fence. I drilled a hole to at the end to attach the shop vacs hose. As we woodworkers tend to do I modified it somewhat by cutting a semi-circle in both the top and bottom pieces for the bit. The purpose is so that I can use this on either side of the fence and still keep the vacuum hose at the rear. Depending on the bit and my feed direction, the auxiliary fence may need to placed on either side of the tablesaw fence. I also added a baffle inside to hep channel the dust into the hose -- worked well, even when cutting all of the flutes on the panel faces!
Things are going nicely on the picture frames. Many, many steps are required to make the 12 sides that are needed to create the 3 frames. I'm making two extra pieces just in case. It's funny how that works, if I make extra parts I never seem to need them but if I don't, then I screw something up -- cheap insurance I guess! Anyway, here's how things are looking now:
The pieces on the left are the panels. Besides cutting to correct size each one needed to have the outer edge shaped and the tongue cut on the opposite edge, this was done on the shaper. Then each needed their 3 flutes cut with the router table that I mentioned above. The pieces on the right will become the sight edge. These had the bead formed on the shaper, a groove for the tongue of the panel, and finally the rabbet was cut for the painting to sit into. Next up is sanding the flutes, planing the faces and then gluing them together as shown in the middle. Let's see, miter, biscuit, glue, clamp, dye, shellac ......... hmm, should be done in a week or two.
Saturday, December 4, 2010
Another Black Frame
Diane's been working on her Square Foot of Art concept where she will paint a series of three related paintings on a 12" x 12" piece of board. One of the series is coffee related and since the painting have lots of texture, she felt the frame should mimic that. Painting it black really isolates the subject. Here's an image of one in that series:
The way I made this frame was to start with a piece of 5/4 Poplar. After shaping the sight edge, the frame was cut at a 10 degree angle. The panel was simply dadoed out to make a shallow groove about an inch plus wide. After mitering and joining the pieces I applied 4 coats of traditional gesso to fill in and obscure the grain of the wood. The final step was to thicken the gesso with more whiting after the last coat, apply that to the panel only and use a comb to give it the texture. It gives the frame movement and life which compliments the pictures nicely. Here's a close up of the frame:
The next set of three will be the steamed Beech, dyed black that I showed a couple of posts ago. Have the material but haven't started cutting into it yet. Good news though, this afternoon I'm off to give a private lesson on using the wood lathe to a man who found me on the internet. Looking forward to it, he just bought a beautiful lathe. I've always thought that I too would like to have a lathe but -- no room and I really want to continue working towards mastering flat work and carving. So much to learn, so little time!
Tuesday, November 30, 2010
Dutch Black Frame Finish
The latest frame escapade has been pursuing how to create a frame finish that replicates the Dutch Black. It's a rich, luster that mimics the originally used Ebony. Ebony is an extremely expensive wood so not an option for creating this finish. I've done other frames by ebonizing them with a vinegar/dissolved metal solution, this reacts with the natural tannins found in the wood and turns the wood black. Although this works well, the color can vary and you need a wood that has a high content of tannin like Oak. For this job, the heavy grain pattern found in Oak wasn't desirable. Of course, another option would be to paint, I've used Krylon and had success with it but just not exactly what I was after.
As I did my research I remembered talking with Peter Werkhoven at the West Coast Framing show last year. Like me, he's a Dutchman so who better to ask for advice! He has his shop in San Francisco, click on this link to go to his website. In any case, he suggested India Ink to blacken the wood followed by French polishing final coats of shellac. Sounded great to me so here's what my sample mold looks like:
Here's what I did to create this molding. First off, it's made of 4/4 Steamed European Beech and about 3" wide. The sight edge is a separate piece that is about an inch tall and currently it's going to be used for panels, not canvas. I used a router bits to cut the grooves and shaped the outer edge and sight edge with a half round profile. Notice that the flat portions have a definite sheen, that's because that surface is hand planed before assembling the frame. The insides of the grooves have a more textural appearance due to the cutting action of the router bit. It's a slight, but obvious, change in texture that adds interest to this molding.
To get the ebony color I used aniline dye (JE Moser) which is something I've always wanted to experiment with. For this mix I used 1 oz. dye, 2 oz. denatured alcohol, and then 6 oz. distilled water. Two applications of the dye with a foam brush a couple of hours apart, wiped dry, and then allowed to dry overnight. I used shellac, a Jathwa button mix, to bring out the color and add a warm amber cast to the piece. This was padded on but next time I think I'll use an airbrush to seal the dye first, followed by the French polishing technique. I had some color transfer on the pad which was more pronounced on the first couple of coats. This may or may not be a problem. In any case, I padded on at least 7 coats and I like the way the planed surfaces have more sheen than the routed grooves. It's finished off with Liberon wax, love the smell and sheen it provides.
Was it successful? well according to my best client/wife it must be because she requested 3, 12" square ones just like the sample for her current Square Foot of Art Series!
As I did my research I remembered talking with Peter Werkhoven at the West Coast Framing show last year. Like me, he's a Dutchman so who better to ask for advice! He has his shop in San Francisco, click on this link to go to his website. In any case, he suggested India Ink to blacken the wood followed by French polishing final coats of shellac. Sounded great to me so here's what my sample mold looks like:
Here's what I did to create this molding. First off, it's made of 4/4 Steamed European Beech and about 3" wide. The sight edge is a separate piece that is about an inch tall and currently it's going to be used for panels, not canvas. I used a router bits to cut the grooves and shaped the outer edge and sight edge with a half round profile. Notice that the flat portions have a definite sheen, that's because that surface is hand planed before assembling the frame. The insides of the grooves have a more textural appearance due to the cutting action of the router bit. It's a slight, but obvious, change in texture that adds interest to this molding.
To get the ebony color I used aniline dye (JE Moser) which is something I've always wanted to experiment with. For this mix I used 1 oz. dye, 2 oz. denatured alcohol, and then 6 oz. distilled water. Two applications of the dye with a foam brush a couple of hours apart, wiped dry, and then allowed to dry overnight. I used shellac, a Jathwa button mix, to bring out the color and add a warm amber cast to the piece. This was padded on but next time I think I'll use an airbrush to seal the dye first, followed by the French polishing technique. I had some color transfer on the pad which was more pronounced on the first couple of coats. This may or may not be a problem. In any case, I padded on at least 7 coats and I like the way the planed surfaces have more sheen than the routed grooves. It's finished off with Liberon wax, love the smell and sheen it provides.
Was it successful? well according to my best client/wife it must be because she requested 3, 12" square ones just like the sample for her current Square Foot of Art Series!
Wednesday, November 24, 2010
Just Keep Learning!
So much to learn in this world I doubt there's enough days left! Here is the completed picture frame and when I mention learning I need to add how to take decent photographs of them. Not too bad but there's room for improvement but since I want to get this published here it is for all to see. I must admit that I'm pleased with the final results of this frame. As I mentioned previously, the design was one that I was inspired to create after seeing a picture of a Frederick Loeser design. The arrows or darts at the corner are a definite Southwestern, Taos style while the curving ribbon between them leads towards the Art Nouveau design. Love to have curling, interwoven designs in my work. One of the things I need to work on though, is refining the background with the chisels. This can be done with sandpaper but that's a long process and I prefer the look of finely cut wood as opposed to sanded/abraded wood. This is in keeping with my previous post of planing the surface of the wood. I've ordered a power honing/sharpening system for the chisels which should make this somewhat easier. The finish is natural Danish Oil which is sanded into the surface. This was followed by wax for protection and to add a sheen to the frame. I believe it will really go well with the Craftsman inspired design of the home it's going to for Christmas.
Speaking of frames, after the Thanksgiving holiday I have a couple of goals lined up. We have a whole bunch of frames that I've carved, designed, and/or gilded. Some of them were created specifically for a painting of Diane's which may have been sold unframed through a gallery. Others were exercises in techniques. In any case, they do take up a lot of space so the plan is to open an Etsy store to sell them at a decent price. Monies will be used to purchase materials to make more frames, buy carving tools, gilding material, and whatever else. Seems as if the more we do, the more we want to improve our craft and this is a means to free up space and purchase more materials. Anyone interested in some frames? I'll put it on my blog as soon as I open the Etsy store.
Speaking of frames, after the Thanksgiving holiday I have a couple of goals lined up. We have a whole bunch of frames that I've carved, designed, and/or gilded. Some of them were created specifically for a painting of Diane's which may have been sold unframed through a gallery. Others were exercises in techniques. In any case, they do take up a lot of space so the plan is to open an Etsy store to sell them at a decent price. Monies will be used to purchase materials to make more frames, buy carving tools, gilding material, and whatever else. Seems as if the more we do, the more we want to improve our craft and this is a means to free up space and purchase more materials. Anyone interested in some frames? I'll put it on my blog as soon as I open the Etsy store.
Sunday, November 21, 2010
Practicing What I Preach
At the last meeting of the Sin City Woodworkers I gave a hands on demonstration on how to set up and use hand planes in our woodworking. You can see the blog here, everyone was asked to bring their own plane and a piece of wood to work on. I think all agreed that it made for a very interesting meeting and I know that personally, as the presenter, I had a great time sharing what I know with the rest of the group.
Currently I'm working on a set of three picture frames for Diane. She has a new series called "A Square Foot of Art" which is a series of 3 separate paintings. I've designed a frame for the first three. Obviously, they are 12" x 12" and the molding I've made is about 3" wide. Here is a shot of the work in progress:
What I wanted to show is how I actually use the plane just as I talked about during my demonstration -- there's no way to get a finer finish than with a nicely sharpened and properly adjusted plane. I mean really, check out those shavings!
Currently I'm working on a set of three picture frames for Diane. She has a new series called "A Square Foot of Art" which is a series of 3 separate paintings. I've designed a frame for the first three. Obviously, they are 12" x 12" and the molding I've made is about 3" wide. Here is a shot of the work in progress:
![]() |
Smooth Plane |
I started this molding with some 5/4 Poplar and cut the beaded profile on the sight edge. The back is cut at 10 degrees to set the frame away from the wall and add some visual depth to the piece. The next step was to use the dado head and cut a shallow (3/32") groove on the face of the molding. At this point you can see the slots for the biscuits which is the way I always join frames; glue, biscuits, and clamp over night. For the finish there will be 4 coats of traditional gesso mopped onto the frame. After the final coat I add more whiting to the gesso to make it quite thick. This thickened gesso will only be put into the shallow groove and then I use a comb on it to give it some interesting texture. Once that's dried completely the entire frame will be sanded. Here's where using the plane to smooth the face and edge is so important. The gesso will telegraph every defect through and it will show. The final finish is black applied over a deep, red base. The technique I use is to allow the black to set up for a couple of days and then use BriWax to carefully cut back the finish and reveal the red base underneath. This replicates the aging process and gives the frame the character Diane is after with her work.
Tuesday, November 16, 2010
Always something to Learn
As the progress continues on the picture frame I've learned a couple of things. One that's not so new is that working with the grain of the wood is crucial and the experience I'm having with this Walnut has taught me I better check the grain of anything I want to carve before I put it together! This piece has some wild grain which changes direction a lot, even within the short 12" or so of molding. File that one away in my memory and hope I retrieve it before I do the next frame.
The other thing occurred by accident. To help me see better when I carve I bought a really nice light from Lamps Plus. It's an LED and gives out a pretty intense light and the color hue can actually be adjusted. I was ready to take a break but forgot to turn off this light at the carving. When I turned off the main light I saw I forgot so went to shut it off. That's when I noticed how the shadows and grain on the frame were much more distinct with the LED light only. Let me illustrate with these pictures:
Notice how distinct the grain of the wood shows up when the main light was turned off? Every little facet shows, see what I mean about the grain being pretty wild in the center? This will be a good challenge and learning (hopefully) experience.
The other thing occurred by accident. To help me see better when I carve I bought a really nice light from Lamps Plus. It's an LED and gives out a pretty intense light and the color hue can actually be adjusted. I was ready to take a break but forgot to turn off this light at the carving. When I turned off the main light I saw I forgot so went to shut it off. That's when I noticed how the shadows and grain on the frame were much more distinct with the LED light only. Let me illustrate with these pictures:
Notice how distinct the grain of the wood shows up when the main light was turned off? Every little facet shows, see what I mean about the grain being pretty wild in the center? This will be a good challenge and learning (hopefully) experience.
![]() |
Main Light Off |
Thursday, November 11, 2010
Frame Project
I've always enjoyed making gifts for those I love, Christmas is one of the prime times to do that. I don't want to let on who this will be for but I know they're not avid Face bookers so it's probably safe to share this project. As usual, this is unlike anything I've attempted before so it's a great big unknown. Diane painted a picture and presented it to these folks so I thought I'd attempt a frame to put it into. It's a fairly small painting and there is a definite Craftsman influence in their home. Dark woods predominate so Walnut is the wood of choice. However; having never carved Walnut for anything serious I know it'll be much more challenging than the Basswood I usually use for picture frames. Even Cherry that I used for the cabinet scraper box is easier to carve than Walnut.
I was inspired by a picture I saw of an art nouveau, Taos style frame created by Frederick Loeser. The size of that frame is 55" x 48" while the frame I'm doing is only 9" x 12" so things needed to be scaled down a lot! I started with a piece of 8/4 Walnut and decided to use the edge grain for my face grain. The pieces I cut off were just under an inch thick and 1 3/4" wide. Here's the first photograph of this project:
I was inspired by a picture I saw of an art nouveau, Taos style frame created by Frederick Loeser. The size of that frame is 55" x 48" while the frame I'm doing is only 9" x 12" so things needed to be scaled down a lot! I started with a piece of 8/4 Walnut and decided to use the edge grain for my face grain. The pieces I cut off were just under an inch thick and 1 3/4" wide. Here's the first photograph of this project:
I put the piece in the middle to show the profile of the molding, nothing fancy with just enough of a rabbet to hold the panel . My method is to make a pattern out of a piece of aluminum valley tin which is what you see laying inside the frame. It cuts easily with my shop scissors and is easily flipped so that both corners can be sketched on. In this case I used a white pencil. Even if the radiuses aren't drawn in exactly it's not too critical since the sweep of the chisel I chose will determine the curve anyway. I've always found the "arrows" at the corners of a Taos/Santa Fe style frame appealing, now you combine it with the art nouveau sinuous curves and I'm really liking it! Have started to carve some of it and just as I suspected the Walnut is a challenge -- why do something easy. Now that it's posted the pressure is on to succeed!
Wednesday, November 10, 2010
Cabinet Scraper Box Finished
Well, here it is my first attempt at some relief carving. I've shown the details of this box in prior posts, it's designed to hold my cabinet scrapers, burnisher, etc. Like many projects it was something I can use in the shop but mainly I wanted to have a practical "practice piece" to play around with and improve my carving technique. You can see the latch on the left side that secures the lid. I added the claws to provide a finger hold to slide the lid open. The other purpose of this box was to experiment with a new type of finish I may want to use on a dining table. I actually hate surface coatings and finish all of my work with a hand rubbed oil which is then top coated with a 3 part concoction I learned about from Art Espinoza Carpenter when I was at San Francisco State. Although it gives a beautiful sheen, it's just not super durable and requires lots of maintenance when used on a surface like a dining table top. What I used here were 3 coats of polyurethane, brushed on and lightly sanded between coats. The problem with a surface coating (other than the plastic appearance) is that it can chip/wear off and also gathers lots of dust during the long drying period. To combat that, this technique uses a gel polyurethane which is basically rubbed on and then wiped off. Although it was a satin it was still too shiny for my tastes so I applied the final two coats with 4/0 steel wool. It's tolerable, next step is to take the sample piece I made and use it at the table to put drinks or plates of hot food on and see if it holds up. All of this for a possible commission somewhere down the road. Never stop learning and trying new stuff!
Monday, November 8, 2010
Whoops !!
We had a family get together last night and I was reminded that I need to post a picture of my grandson in his crib -- like the saying goes "my bad". Here it is, isn't he a handsome boy!
Sunday, October 31, 2010
My 100th. Post!
When I first began this blog I didn't know how far it would go and how long I'd last doing it but here it is, post number 100. Never know how many readers I actually have but since there has been a fair amount of feedback, questions, and comments it's been worthwhile to me. Hopefully the goal of sharing my woodworking trials and tribulations have encouraged others to try the craft. Learned a long time ago that you can't get anywhere if you're just sitting on the couch! Yesterday Diane and I went to the Civil War reenactment at Spring Mountain ranch. I had my sample pistol case and flyers to see if I could generate some potential commissions and she had her camera to see if she could capture some good images to use as reference material for future paintings. Other than the occasional wind gusts the weather was pretty nice and we made some contacts.
Earlier I'd mentioned that I have a couple of projects in the works. One of them are the two frames I'm currently gilding and one of those is just about complete. The other I'll try to improve what I did on this first one -- it's a definite work in progress this business of gilding. The other is the box to hold my cabinet scrapers, files, burnishers, etc. Here's how it looks at this time:
This a practical project and it's allowed me to experiment with some techniques as well. First off is the carving. The profile of Ali is pretty self explanatory but now I've added her paws. They're a little over sized but were added so that I could get a grip on the sliding top to open the box -- Ali agreed to pose for them. To finish this box I plan to use a new process I read about that (hopefully) should be a durable one for a dining table top. The hand rubbed finish I've been using for years on my furniture is not as durable as I'd like for that and requires some maintenance. Supposedly, this finish will appear as a hand rubbed one but uses gel polyurethane rather than my concoction of linseed oil, turpentine, and varathane as a final coat. I'll keep you posted.
Earlier I'd mentioned that I have a couple of projects in the works. One of them are the two frames I'm currently gilding and one of those is just about complete. The other I'll try to improve what I did on this first one -- it's a definite work in progress this business of gilding. The other is the box to hold my cabinet scrapers, files, burnishers, etc. Here's how it looks at this time:
![]() |
Scraper Box in Progress |
Wednesday, October 27, 2010
What's New in the Shop
Now that I've had the chance to see my new grandson life is back to normal -- sorta! I don't know if I'll ever become a proficient gilder, it's a difficult art but I keep plugging away. I've just used up 11 of the 20 books of gold and do have quite a number of frames to show for it. While in Seattle, I visited Charles Douglas at his Gilding Studio. We had a nice visit and I would like to take one of his 3 day workshops to get more one on one instruction on laying the gold. Practice, Practice, and more Practice is what it will take. A pack of 22 kt. gold is about $400.00 and has those 20 books. Although it's expensive, the gold is really a minor part of the operation. The preparation of the frame with 6-8 coats of gesso followed by the same number of coats of bole (clay), not to mention any carving I might try to throw in is where the cost comes in. Thankfully my labor is pretty reasonable, truth be told I couldn't afford myself! Here is a picture of two small sample pieces I'm doing at the same time, they'll be used to experiment with the toning process once I complete the two 16 x 20 frames that are in the works.
It's hard to tell but the cut off piece on the left has some combed gesso, a process I've always wanted to try. Just as the name implies, I made the gesso fairly thick and then used a comb to create the texture, it should make for an interesting frame. The longer piece has composition ornamentation on it and is what the frame I'm almost done gilding has. The molding is modified from our stock and then I steamed on the "fish scale" pieces all the way around. It's destined for a painting Diane did based on a photo she took at Pike's Market when we visited there last year. Anyway, once it's done I'll post it on the blog.
It's hard to tell but the cut off piece on the left has some combed gesso, a process I've always wanted to try. Just as the name implies, I made the gesso fairly thick and then used a comb to create the texture, it should make for an interesting frame. The longer piece has composition ornamentation on it and is what the frame I'm almost done gilding has. The molding is modified from our stock and then I steamed on the "fish scale" pieces all the way around. It's destined for a painting Diane did based on a photo she took at Pike's Market when we visited there last year. Anyway, once it's done I'll post it on the blog.
Monday, October 25, 2010
My Review of PFEIL "Swiss Made" Undercutting Tool Left
Originally submitted at Woodcraft
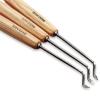
Character limit per line: 30
Just Right!
By Woodworks by John from Las Vegas, NV on 10/25/2010
5out of 5
Pros: Work in restricted space, Works Effectively
Best Uses: Small detailed carvings
Describe Yourself: Professional
Primary use: Personal
I found these very useful for the small areas that are carved into my picture frames. The "dog leg" design keeps the handle out of the way and allows you to cut to your design or stop cut. They make a strange sound as you cut because of flex in the shaft where it makes the "dog leg". My designs are low relief but these chisels could reach down into a pretty deep space. A little tricky to sharpen but I'm pleased with the set.
(legalese)
Saturday, October 16, 2010
One of Two Projects in Progress
![]() |
Carved Lid for Tool Box |
It's made of materials I had left over in the shop and it's the finger jointed, Oak box that you see in the background. The lid slides in and is made of Cherry that has been resawn and turned into a book matched panel. The image is of Ali, my buddy -- she's an Oriental Shorthair and this is how she spends much of her day, splayed out on top of the couch watching over the house. She's a really cool cat but like my father in law says: "jeez, don't get him started on that d#%&* cat!". Suffice to say she's truly captured my heart and made me her chosen one.
The other thing I want to experiment on with this box is a finish I've read about that is better suited for dining tables. Less maintenance than the finish I've always used. Basically it's several coats of polyurethane brushed on, then lightly sanded and followed by hand wiping gel polyurethane onto the surface. Although I stay away from surface coatings and prefer to hand rub in oil and my own top coat concoction this should stand up better to a surface like a dining table that is subject to spills. Time will tell and I'll share the results.
Wednesday, October 6, 2010
Saturday, September 25, 2010
Barstools project Completed
I had the phone call yesterday I've been waiting for from Niagara Upholstery here in Las Vegas to tell me the work was done. I picked them up this morning and the work John did was excellent. Definitely will use him again and recommend his work to anyone. Here are a couple of shots of the completed stools, I'm pleased with the results. The over-all height is about 42" with the seating being approximately 16" square. Top of the cushion is at 32" which should be just right for my clients counter height.
![]() |
3/4 View showing the grid and footrest |
![]() |
Head on View |
Saturday, September 18, 2010
Making a Spokeshave
I've always been intrigued with the thought of making my own tools, sure, we woodworkers often make jigs to help build projects but making a tool is another thing. At the beginning of this year I used a gift certificate from Lee Valley to buy their small, spokeshave kit. I regularly use a metal Stanley #151 in my work to ease corners and put chamfers on the ends of pieces but thought that a small, wooden bodied spokeshave would be just the right challenge for my first, shop made tool. Here's a picture of the final result:
After gluing the blank together you need to drill and tap holes for the adjustment screws to thread into the wood. Obviously, these must be perfectly square and aligned to the body. The kit even supplied the tap needed. In this first picture, the holes are drilled and taped and I'm preparing to cut out the angled section for the ware. The tape was to see the line better, I made a series of cuts with the dovetail saw which were then chiseled out.
Once the ware was correctly sized the next step was to insert the blade into the body. It needed to be recessed so that it was flush with the bottom of the body. You can see the brass piece that will become the wear strip at the front of the blade.
Next was to fit the brass wear strip in front of the blade. The ends are dovetailed into the body at about 10 degrees and the strip is also filed to a 45 degree angle to match the ware. Once the clearance between the blade and wear strip was correct holes were drilled and the entire wear strip was filed and shaped to fit flush into the body.
Now comes the final cutting and shaping of the spokeshave. I learned a technique where you use a glue stick to attach the pattern to the wood, it's very easy to remove with a scraper. I also drilled holes for the area where you put your thumbs when using the shave. Much easier to drill a radius than it is to cut one, a forstner bit worked well for this.
I made it out of 2 pieces of Chakte Kok with a strip of Australian Lacewood in the middle. In retrospect, the Chakte Kok may be a little soft as it chipped ever so slightly at the ends of the wear strip. An advantage to this kit is that it came with enough of the brass wear strip to make another spokeshave body. I used water stones to sharpen the blade and the cut it makes is nice. There will be a learning curve to using this though. I'm accustomed to pulling a spokeshave towards me but am finding that this works better when it's pushed away. This project was pretty time consuming and required lots of thought and precision. I worked on it between other projects and enjoyed the process -- even when I'd make the occasional mistake like grabbing a 7/32" bit instead of a 7/64"! What the heck, a little dowel, a little epoxy, and you'd never know it happened.
After gluing the blank together you need to drill and tap holes for the adjustment screws to thread into the wood. Obviously, these must be perfectly square and aligned to the body. The kit even supplied the tap needed. In this first picture, the holes are drilled and taped and I'm preparing to cut out the angled section for the ware. The tape was to see the line better, I made a series of cuts with the dovetail saw which were then chiseled out.
![]() |
Cutting the Ware |
![]() |
Blade recessed into the Body |
![]() |
Wear Strip Installed |
![]() |
Pattern in place, ready for the Bandsaw |
After filing and sanding to get the final shape, one that felt good in my hands I used the 3 part, top coat finish I use on my furniture. First coat wet sanded with 220, followed by successive coats with 400 and 600 grits. After honing and sharpening the blade it was time to test it out. Here's a couple of photos of the results on a piece of hard Maple. I'd suggest taking this on for your first, shop made tool if you should get the urge! Glad to answer any questions if you run into a problem.
![]() |
Rounding over the Edge |
Sunday, September 12, 2010
Finishing Time
When you work towards this part of the project it gets quite rewarding. Now is when you can tell if your planning, scraping, and sanding achieved what you were after. Must admit that I'm happy with what I see. Much of the grain in the Maple actually looks like marble and even though most folks won't notice, it excites me! This morning I sanded in the second top coat with the 400 grit paper. Each coat takes about an hour to apply and needs to cure for 24 hours before the next is applied. Tomorrow will be the first of two additional coats with 600 grit paper which will be followed up by the final coat applied with denim. In the photo you can see the two footrests and grid assemblies which will be attached after the denim coat. They're resting on the seat cushions. After my doctors appointment tomorrow I plan to go to Tandy to pick out the leather for them. Finishing items like stools or chairs is pretty time consuming because of all the right angles where stretchers meet the legs. Terrible places for the finish to collect and leave a rough spot that needs to be removed later with a little bit of turpentine. Wipe, wipe, and then wipe again -- I'm anxious to get these finished and delivered. I really like the way the polished copper and the Chakte Kok grid and back go with the Maple.
Tuesday, September 7, 2010
A Little Philosophical
There were two things that happened recently that have made me somewhat philosophical as I look at this woodworking I enjoy so much. Maybe I've just had too much time to think as I lay on the couch, icing my knee, and keeping it elevated so that this swelling will go down once and for all and I'll be back to being somewhat normal again. In any case, here's the deal.
In a recent newsletter from Fine Woodworking they talked about how computer controlled woodworking is coming to the small home and professional shop. Just like any other technology the price has come way down. This opened a discussion as to whether or not we (fine woodworkers) would embrace it or say that it belongs in manufacturing only. Several had put their two cents in and I'm still deciding if I want to or not. Technology is pretty much about doing things faster, repetitively, and accurately -- bottom line for me is GREED! One person made the point that if we can produce things quicker we are also using our natural resources up quicker which really goes against the whole green movement. My personal feelings are that the process of designing and making "stuff" is what brings satisfaction. Saying that though, I also realize that to make money you need speed and efficiency and technology can give that to you.
The other thing that happened is that a couple of my neighbors came over and asked how long I've been working on the stools. In spite of the movement limitations caused by the knee surgery I told them about 40 hours. Now that's quite a while, especially to the 20 somethings who are accustomed to the microwave society and instant everything. They did admire the work though.
Here's a little photo essay to help illustrate some of the process. I'm currently fitting the curved backs to the square uprights of the stool.
In a recent newsletter from Fine Woodworking they talked about how computer controlled woodworking is coming to the small home and professional shop. Just like any other technology the price has come way down. This opened a discussion as to whether or not we (fine woodworkers) would embrace it or say that it belongs in manufacturing only. Several had put their two cents in and I'm still deciding if I want to or not. Technology is pretty much about doing things faster, repetitively, and accurately -- bottom line for me is GREED! One person made the point that if we can produce things quicker we are also using our natural resources up quicker which really goes against the whole green movement. My personal feelings are that the process of designing and making "stuff" is what brings satisfaction. Saying that though, I also realize that to make money you need speed and efficiency and technology can give that to you.
The other thing that happened is that a couple of my neighbors came over and asked how long I've been working on the stools. In spite of the movement limitations caused by the knee surgery I told them about 40 hours. Now that's quite a while, especially to the 20 somethings who are accustomed to the microwave society and instant everything. They did admire the work though.
Here's a little photo essay to help illustrate some of the process. I'm currently fitting the curved backs to the square uprights of the stool.
![]() |
Dovetail Saw and Flush Saw used to cut an angled notch. |
![]() |
Back is carefully laid out and notch is pared to match the curve of the back using spokeshave and chisel. Tape is used to locate the center of the back in stool. |
The final steps were to drill the holes in the back and then counterbore them for the maple plug that will conceal the screw. You'll notice that the back also has a couple of wash coats of shellac on it to seal wood since the Chakte Kok dust can actually be used as a bright, red dye. Next in line is the finish of the stools which will be done after final scraping/sanding and forming chamfers on the edges. After the oil has dried overnight the backs will be epoxied and screwed on, maple button epoxied to cover the screw head and then chiseled flush. Finally the top coats (5-6) will be hand sanded in to achieve the finish I'm somewhat known for and ...... oh yeah, still need to get the leather and upholster the seats -- whew!!
So, could a batch of computer operated machines have done this faster? Probably, would the project mean as much to my client? I'd like to think not. The appeal of artfully designed objects is that they are unique and tailored to meet what you like. You're not going to walk into your neighbors house and see the exact same thing. Just like I used to customize cars and motorcycles so that they were one of a kind and unique to me and my personality. Faster is not always better, when I look at our society in general I always remember what Diane once said: " even though we have hundreds of labor saving devices, no one seems to have time for anything anymore". Okay, guess it's time for an ibuprofen and leg elevation!!
Friday, September 3, 2010
How Many Clamps does it take ...........?
The usual answer to that is "one more than what you have"! I was so lucky and blessed to have these clamps donated to me from Bob, I mean, they were exactly what I needed complete the laminations for the bar stools. Wonderful, heavy duty clamps unlike the majority of what you find these days that flex, slip, and just don't grip. Most of my own clamps are those that I've picked up through the years from school shops that have gone by the wayside as well as long established woodworking shops that have had to close. They may weigh a ton but boy do they do the job. Here's what I'm talking about:
The jig took about 10 hours total to make but works well, I've got my fingers crossed that my client will decide to have me do 4 more chairs and a dining table for him as well. I just so happen to have enough Chakte Kok and Maple pieces milled down for 5 more backs like this.
Each back consists of 4 pieces, in spite of the swollen knee and foot I was able to stand for the time it took to glue them up early this week when the weather was so cool in the morning. Temperature makes a difference in how much open time you have with the Plastic Resorcinol Glue. The process is to use a small roller, apply glue to both sides of each piece (except for the front/back), sandwich them together, wrap them in wax paper, and stick them into the form. The biggest improvement on this jig is being able to get clamping pressure on the bottom of it. This was accomplished with the holes in the male portion and the deep F-clamps. Once the pieces are in the form I lay the 2 bar clamps across the top and start to bring them together. Under the F-clamp in the center is a center line I use to keep things lined up. I've found that it's best to start from the center and then work out to the outsides. They all need to be tight but you have to keep in mind that they also slide against each other as they're forced into the curvature. Once everything is tightened in sequence I let it dry at least 24 hours, no sense rushing it.
Both of the backs are done and one edge has been scraped of glue and hand planed square. My next step is to bring the other side parallel on the tablesaw but I'm afraid I don't have the stability in my leg yet to operate the saw safely. Sure am glad my client hasn't put a deadline on this project. Bending wood is a cool process. As you can tell though, it's not a quick and easy one, hey; if it was easy everybody would do it!
![]() |
Seat Back Lamination Jig |
Each back consists of 4 pieces, in spite of the swollen knee and foot I was able to stand for the time it took to glue them up early this week when the weather was so cool in the morning. Temperature makes a difference in how much open time you have with the Plastic Resorcinol Glue. The process is to use a small roller, apply glue to both sides of each piece (except for the front/back), sandwich them together, wrap them in wax paper, and stick them into the form. The biggest improvement on this jig is being able to get clamping pressure on the bottom of it. This was accomplished with the holes in the male portion and the deep F-clamps. Once the pieces are in the form I lay the 2 bar clamps across the top and start to bring them together. Under the F-clamp in the center is a center line I use to keep things lined up. I've found that it's best to start from the center and then work out to the outsides. They all need to be tight but you have to keep in mind that they also slide against each other as they're forced into the curvature. Once everything is tightened in sequence I let it dry at least 24 hours, no sense rushing it.
Both of the backs are done and one edge has been scraped of glue and hand planed square. My next step is to bring the other side parallel on the tablesaw but I'm afraid I don't have the stability in my leg yet to operate the saw safely. Sure am glad my client hasn't put a deadline on this project. Bending wood is a cool process. As you can tell though, it's not a quick and easy one, hey; if it was easy everybody would do it!
Wednesday, September 1, 2010
TV Lift Cabinet -- DONE!
In spite of being on crutches and unable to drive, last night the cabinet was completed. There was no way I could of done it without Adam's help. He came over after work, loaded the needed parts and tools (including me!) to finish it into the van and away we went. Thankfully, the guy who did the beautiful faux finishing on it delivered straight from his studio to the client. Although the French Provincial style isn't one that I'd personally select for my own house I'm proud of the way this entire cabinet turned out and learned a lot from it. That's the upside to doing one of a kind pieces, seems as if there is always something you learn that you can apply to other challenges as they come up. When I look back at the initial sketch that Durette Studio sent for me to bid on I think it came out remarkably well!
The composition ornamentation really shows how dimensional it is in this view. Some of the largest work I've done but so much easier and quicker than hand carving all of this detail. Adam and I installed the television as well and the mechanism from Nexus is a quiet, smooth operating piece of equipment. When we first tried the swivel action, it seemed to stop at about 95 degrees -- not a good thing. Ron decided to give just a bit more effort and in spite of making some strange noises the unit swiveled like it was supposed to. After that I remembered reading in the manual that the first swivel or two may be difficult as the bearings need to set in.
All in all, this was a good project, one I'm glad to have taken on and completed.
![]() |
Frontal View |
![]() |
Side View |
The composition ornamentation really shows how dimensional it is in this view. Some of the largest work I've done but so much easier and quicker than hand carving all of this detail. Adam and I installed the television as well and the mechanism from Nexus is a quiet, smooth operating piece of equipment. When we first tried the swivel action, it seemed to stop at about 95 degrees -- not a good thing. Ron decided to give just a bit more effort and in spite of making some strange noises the unit swiveled like it was supposed to. After that I remembered reading in the manual that the first swivel or two may be difficult as the bearings need to set in.
All in all, this was a good project, one I'm glad to have taken on and completed.
Monday, August 30, 2010
Latest Picture Frame for Diane
At the beginning of this summer we took a trip to Seattle to deliver the crib for my soon to be, grandson. That was a great visit and one of the places we went to was the Center for Wooden Boats. I'd heard about them through woodworking magazines so the four of us went to check them out. It's a combination museum and woodworking school, heck, they're even listed in Wikipedia! Rich has sailing experience and he said that for sure, him and Jennifer would be back to see about renting a sailboat in the future. There were a couple of guys working in the shop and it was great to see all of the old hand tools being used as intended. The walls also had these hull sections showing the profile at various points along the length of the ship. Upstairs there is a school, library, and examples of wooden boats and assorted paraphernalia. On the docks there are a number of boats. If you're ever in the area, it's located on Lake Union and is a wonderful place to visit.
Diane snapped a number of pictures and when we returned home this is one she began on. You're looking out of a window but the ship is a model, perhaps of one that is still to be built. The shop itself oozed character, open framed walls, rough cut studs, pots and containers of who knows what, things hanging off nails stuck into the wall, and of course the tools set on any available surface. Here's what the painting looks like:
Diane snapped a number of pictures and when we returned home this is one she began on. You're looking out of a window but the ship is a model, perhaps of one that is still to be built. The shop itself oozed character, open framed walls, rough cut studs, pots and containers of who knows what, things hanging off nails stuck into the wall, and of course the tools set on any available surface. Here's what the painting looks like:
The frame is made of Walnut, I cut a triple bead detail on my shaper and then resawed the remainder of the 5/4 material to make the panels. Finish is natural oil and the painting is 20" x 24". The molding itself is 5" wide. It has been accepted into the Oil Painters of America Western Show which will be held in Jackson, WY this fall. Seems like an awfully good reason for a road trip!
Monday, August 23, 2010
Stools Assembled
This morning I decided to take the chance that it wouldn't be too hot and I'd be able to get the stools assembled -- good idea because it went pretty smoothly. Here is a picture of them with the clamps still on them. I prefer leaving clamps on 24 hours even though I know a couple of hours should be sufficient -- another reason I like working on singular projects as opposed to production work with deadlines! Here's the photo:
I couldn't resist laying the grid in place on the bottom to get a visual of how it will all come together. I can picture the copper being highly polished and then the contrast of the curved back it should be awesome.
The next step is to glue up the laminations for the back. All of the pieces are ready to go, I just need to have the weather cooperate. Each back consists of 4 pieces, 3/32" thick so that means 6 surfaces that measure about 3" x 28" that need to have glue applied, wrapped in wax paper, and put into the form all before it starts to set! Laminating requires resorcinol glue which needs to be mixed fresh before glue up. I'm thinking of maybe covering the island in the kitchen, throwing down some drop clothes, and doing the glue up in the house. Betcha I can talk Diane into it, heck I know she'd help me if I need it. I always get somewhat stressed during glue ups anyway.
Let me share a construction detail with you. This is what I did on the bottom of each leg, a very slight chamfer that serves two purposes. First off I think it adds a small detail and makes it appear as if the stool is "floating", then, from a construction stand point it will prevent the grain from splitting should the stool be dragged across the floor. I have some glides from Lee Valley Hardware that lift the stool up ever so slightly and are designed for tile or wood floors.
I couldn't resist laying the grid in place on the bottom to get a visual of how it will all come together. I can picture the copper being highly polished and then the contrast of the curved back it should be awesome.
The next step is to glue up the laminations for the back. All of the pieces are ready to go, I just need to have the weather cooperate. Each back consists of 4 pieces, 3/32" thick so that means 6 surfaces that measure about 3" x 28" that need to have glue applied, wrapped in wax paper, and put into the form all before it starts to set! Laminating requires resorcinol glue which needs to be mixed fresh before glue up. I'm thinking of maybe covering the island in the kitchen, throwing down some drop clothes, and doing the glue up in the house. Betcha I can talk Diane into it, heck I know she'd help me if I need it. I always get somewhat stressed during glue ups anyway.

Thursday, August 19, 2010
The Business of Custom Work
As I've been working in the shop these past couple of days, things have been going around in my head! Maybe it's the 100+ degrees, high humidity, or the Woodshop News article asking how we're coping with the record heat this summer. Don't get me wrong, this isn't a rant, just miscellaneous observations I've made these past days. Doing custom work, creating one of a kind pieces just can't be compared to the mass produced (mostly Chinese these days) offerings you find in any of the big box stores and even many of the so called "high end" furniture stores. We had a demonstration last night on using Google Sketch Up to design projects. I hate to sound like a dinosaur because I know that it definitely has it's place but I couldn't help but think how computers can stifle your creativity. Similar to the feelings I had when calculators first came into the schools. They're great tools to speed up your math process but if a student didn't understand the process in the first place it becomes a crutch for them and the problem is that they fail to grasp whatever concept there is. They knew that Mr. Eugster didn't allow plastic brains! The problem I'm ranting (whoops, said this wasn't one) about is that the average person doesn't understand what goes into making the items we use everyday. With a program like Sketch Up you sketch what you'd like and "it" designs it. You can then take this sketch, put it into a program, and your parts can be made from metal, wood, glass, etc. just by computer control.
Let me use the grid I'm making for the bottom of the two bar stools I've been commissioned to make. On the surface this looks pretty straight forward, the two maple pieces at the ends or the stretchers for the stools themselves while the grid of Chakte Kok is not only a decorative element but supports the foot rest at the front. A 1" copper pipe will be attached to those half round recesses for that purpose. What you may not realize (or care about) is the setups and time it takes to create the lap joints holding the grid together, then drilling counter bores and pilot holes for the screws which will be hidden or plugged. This requires careful measurement and inventing ways to make the cuts all the same on each piece. Then there's the tenons at each end of the stretcher and the chamfers I cut on the ends of each piece as a style element and also to minimize splitting on the ends of the pieces.
To cut all of those chamfers I made this jig and guide block to have some control. When only a couple of chamfers are needed it's easy enough to eyeball them but with multiples it's best to make a jig. When your mindset is to "let the computer" do the design work then you're at "its" mercy and limited by what it's programed to do. If, on the other hand, you understand the problem, then you can figure out how to solve it based on experience.
So, what's my bottom line, purpose behind my blog today?, not really sure! Must be the heat because when I know I truly enjoy the work and process behind making things. I'm afraid that much of what I do is a dying art. My last years teaching woodshop showed me that these traditional skills, those that take time and effort to perfect are not that appealing to the general public. I hope this art form will never be lost. Diane and I like to watch American Pickers. A recent conversation we had is what will happen when the people that can recognize "junk" that we produced here are gone? Who will carry on that tradition of knowing that the engine block you found is one of a few produced and worth thousands?

Let me use the grid I'm making for the bottom of the two bar stools I've been commissioned to make. On the surface this looks pretty straight forward, the two maple pieces at the ends or the stretchers for the stools themselves while the grid of Chakte Kok is not only a decorative element but supports the foot rest at the front. A 1" copper pipe will be attached to those half round recesses for that purpose. What you may not realize (or care about) is the setups and time it takes to create the lap joints holding the grid together, then drilling counter bores and pilot holes for the screws which will be hidden or plugged. This requires careful measurement and inventing ways to make the cuts all the same on each piece. Then there's the tenons at each end of the stretcher and the chamfers I cut on the ends of each piece as a style element and also to minimize splitting on the ends of the pieces.
To cut all of those chamfers I made this jig and guide block to have some control. When only a couple of chamfers are needed it's easy enough to eyeball them but with multiples it's best to make a jig. When your mindset is to "let the computer" do the design work then you're at "its" mercy and limited by what it's programed to do. If, on the other hand, you understand the problem, then you can figure out how to solve it based on experience.
So, what's my bottom line, purpose behind my blog today?, not really sure! Must be the heat because when I know I truly enjoy the work and process behind making things. I'm afraid that much of what I do is a dying art. My last years teaching woodshop showed me that these traditional skills, those that take time and effort to perfect are not that appealing to the general public. I hope this art form will never be lost. Diane and I like to watch American Pickers. A recent conversation we had is what will happen when the people that can recognize "junk" that we produced here are gone? Who will carry on that tradition of knowing that the engine block you found is one of a few produced and worth thousands?
Sunday, August 15, 2010
Machine Part of Joinery Done
Although I always use traditional joinery in my work, machines do play a very important role. It's not my quote but it was said by another woodworker that he uses his machines just as a craftsman of old used their apprentice! In other words, they do the repetitious grunt work so I can concentrate on refining the joints with chisel, saw, plane, etc. to bring it all together. So where I use my surface planer to bring pieces to their required thickness, it's using the smooth plane that eliminates the marks left by the machine and prepares the stock for finishing. I suppose the big difference is that eventually the apprentice would become a craftsman where the machines will quietly and efficiently do their work asking only for their required maintenance -- I can deal with that!
Previously I'd mentioned how it's crucial to make a full size drawing of chair parts and then taking sizes and angles off of that, here's a photo:
There's a bit of distortion so you'll have to take my word for it that the piece of wood is the exact size and angle as what's been drawn. At this point the tenons are the same width as the stretcher but they will be trimmed to fit into its mating mortise. This will be accomplished with a dovetail saw, chisel for paring, and a rabbet plane. Lately I've been cutting my tenons with two dado blades with spacers in between them to match the mortise width. That way you only make one pass on the saw with the tenoning jig for each end. I leave them ever so slightly over sized and then use the rabbet plane to not only fine tune them but also to smooth the cheeks for a better gluing surface.
Tomorrow I plan to fit all of them, start on the grid for the bottom, and begin shaping the legs with a spokeshave. As luck would have it the weather man has predicted more heat -- bad timing! When I laminate the back I need as much time as possible to spread the glue on all of the pieces, can't have it setting up before I get them into the form and clamped. Hopefully too, some time this week I'll get a call from the finisher telling me that the TV lift cabinet is ready for it's final assembly. Be glad to write "Completed" next to that project.
Previously I'd mentioned how it's crucial to make a full size drawing of chair parts and then taking sizes and angles off of that, here's a photo:
There's a bit of distortion so you'll have to take my word for it that the piece of wood is the exact size and angle as what's been drawn. At this point the tenons are the same width as the stretcher but they will be trimmed to fit into its mating mortise. This will be accomplished with a dovetail saw, chisel for paring, and a rabbet plane. Lately I've been cutting my tenons with two dado blades with spacers in between them to match the mortise width. That way you only make one pass on the saw with the tenoning jig for each end. I leave them ever so slightly over sized and then use the rabbet plane to not only fine tune them but also to smooth the cheeks for a better gluing surface.
Tomorrow I plan to fit all of them, start on the grid for the bottom, and begin shaping the legs with a spokeshave. As luck would have it the weather man has predicted more heat -- bad timing! When I laminate the back I need as much time as possible to spread the glue on all of the pieces, can't have it setting up before I get them into the form and clamped. Hopefully too, some time this week I'll get a call from the finisher telling me that the TV lift cabinet is ready for it's final assembly. Be glad to write "Completed" next to that project.
Saturday, August 14, 2010
Bloodwood vs. Chakte Kok
As I mentioned in an earlier blog I (and my client) just wasn't pleased with the coloration of the Bloodwood. What I had shown him was a piece of Chakte Kok and even though the Bloodwood is a good looking piece of wood it doesn't have the pizzazz of the Chakte Kok. I learned that it is sometimes referred to as Red Heart and when you look at this picture you can see why:
That's the Bloodwood on the left and the Chakte Kok on the right. It will be used for the curved and laminated back rest and also combined used in a grid at the bottom of the stool that will have a section of copper pipe and serve as the footrest.
That's the Bloodwood on the left and the Chakte Kok on the right. It will be used for the curved and laminated back rest and also combined used in a grid at the bottom of the stool that will have a section of copper pipe and serve as the footrest.
Saturday, August 7, 2010
Thanks Bob Z!
You may remember a post where I mentioned that I'd received a call from a gentleman regarding some tools he wanted to give me. Just to recap, he's retired and did an apprenticeship in Sweden in the 60's and had been moving these tools around with him ever since. When he saw the chair publicity in the newspaper he and his wife decided that his tools would serve me well and they were right! I've given some away to other, like minded woodworkers, and kept the others. One of the ones I've kept is this wooden smoother plane.
I've always wanted to try one out and the feel is quite different from the bronze, #4 I have from Lie-Nielson. Currently I'm working on some picture frames for Diane and this Walnut panel is for one of them. After sharpening the blade I was eager to try it out. Your hand position is different from a metal bodied plane. The left hand wraps around the horn while your right hand wraps around the back section just below the blade. The most obvious difference is how this plane is adjusted. The mallet in the background is used to tap either the blade or a designated spot at the rear of the body -- a metal button to set the blades depth and level it. Just like everything else, there's a learning curve and I doubt I've mastered it at this point!
Using the plane was nice, totally different feel to it but as you can see by the thin shavings it worked out well for me. Nothing like using a sharp blade to get rid of the chatter marks a planer will always put on the surface. Another plane I'm holding on to is a bullnose that's over 1 1/2" wide and will be a good choice for trimming tenons. I'm currently sharpening that one (needs a lot of work) and will try it out on the tenons for the bar stool. Had a minor setback on that project, the Bloodwood they sent doesn't have the brilliant red color like the Chakta Kok I showed for the barstools. Currently Woodworkers Source is out of stock but thankfully, the client for those is not in a hurry.
I've always wanted to try one out and the feel is quite different from the bronze, #4 I have from Lie-Nielson. Currently I'm working on some picture frames for Diane and this Walnut panel is for one of them. After sharpening the blade I was eager to try it out. Your hand position is different from a metal bodied plane. The left hand wraps around the horn while your right hand wraps around the back section just below the blade. The most obvious difference is how this plane is adjusted. The mallet in the background is used to tap either the blade or a designated spot at the rear of the body -- a metal button to set the blades depth and level it. Just like everything else, there's a learning curve and I doubt I've mastered it at this point!
Using the plane was nice, totally different feel to it but as you can see by the thin shavings it worked out well for me. Nothing like using a sharp blade to get rid of the chatter marks a planer will always put on the surface. Another plane I'm holding on to is a bullnose that's over 1 1/2" wide and will be a good choice for trimming tenons. I'm currently sharpening that one (needs a lot of work) and will try it out on the tenons for the bar stool. Had a minor setback on that project, the Bloodwood they sent doesn't have the brilliant red color like the Chakta Kok I showed for the barstools. Currently Woodworkers Source is out of stock but thankfully, the client for those is not in a hurry.
Thursday, August 5, 2010
Barstool Joinery
The TV lift cabinet went to the finisher today so now I have room in the shop to spread out and begin some serious work on the barstools. Up to this point I've made the form to laminate the back, ordered and picked up the Bloodwood for the back and the lower grid, and roughed out the Maple for the legs. One of the most difficult aspects of building a chair or a stool is the joinery. Since my objective is to build heirloom quality pieces I stay with traditional methods. In the world of woodworking certain things "say" quality. One of the most obvious ones is using dovetails, they are a hallmark of fine furniture construction. Among furniture, chairs are one of the most difficult items to make because of the angled joinery. Other areas that are pretty complex are circular stairs and wooden boats -- haven't tackled those yet!
As far as chairs go, a tried and true method to tackle the joinery is to make full size drawings and then use a bevel to establish your angles. In this photo, I've done just that:
This is one area where "winging it" can get you into trouble! What is drawn is half of the chair, the mortises are drawn in to locate them exactly. Chairs take a lot of stress so the design and placement of the joinery need to take that into consideration. Mortises have been cut for the stretchers and the bottom foot rest. One of the design decisions I can make is choosing the wood and the surfaces that will show. At the left are the front legs for one of the chairs and although it's pretty difficult to see from this photo they are cut from the same board and the bottom portion has that waterfall grain effect. Those are the little things that separate a custom piece from a factory made project -- it's good to be able to take the time and care required.
As far as chairs go, a tried and true method to tackle the joinery is to make full size drawings and then use a bevel to establish your angles. In this photo, I've done just that:
This is one area where "winging it" can get you into trouble! What is drawn is half of the chair, the mortises are drawn in to locate them exactly. Chairs take a lot of stress so the design and placement of the joinery need to take that into consideration. Mortises have been cut for the stretchers and the bottom foot rest. One of the design decisions I can make is choosing the wood and the surfaces that will show. At the left are the front legs for one of the chairs and although it's pretty difficult to see from this photo they are cut from the same board and the bottom portion has that waterfall grain effect. Those are the little things that separate a custom piece from a factory made project -- it's good to be able to take the time and care required.
Monday, August 2, 2010
Composition Ornaments are Done
Here we have it, the final design of the ornamentation. I'll allow it to dry thoroughly over night and then use a scraper to eliminate the "ghost" patterns where the compo left its' tracks. It's hard to make out in this picture but there is a line of compo that finishes the bottom curve nicely. If you've never worked with this stuff it's pretty neat. This was really fresh so didn't take too much time on the steamer to activate the glue. Just like anything else, there is a learning curve. I did the sides first, then the back, and left the front for last. A friend of mine came over to see how to work with it and even though he's a carver could see the value in using the compo -- imagine how long it would take to carve all of this by hand? Like he said, maybe Christmas; yeah, 2011 ! The next step will be getting it to the finisher so he can work his magic to make this piece look like an antique, French Provincial chest. After I clean up any little details, tape off the lift mechanism, and organize the inside wiring it'll be ready for the finishing process.
Tuesday, July 27, 2010
Publicity Helps
Two really good things happened after the article about the Dovetail Chair appeared in the newspaper. One was that I got a telephone call from a gentleman offering me some of his tools! Without boring you with the details, basically he hasn't been able to use them for many years. He's now retired and living in a condominium and wouldn't have the space to work anyway. He was trained in Sweden and knew James Krenov. If you're not familiar with him, Google his name as he was a great influence and educator here in the US. Unfortunately he passed away not too long ago but his influence will last for a long time, he started the College of the Redwoods in Fort Bragg, CA which is a top notch woodworking institution. In any case, I was given stewardship of several Swedish wooden planes, clamps, and a Stanley #4C. I've already given some of it away to a woodworker I know that has the same philosophy towards the craft and using hand tools. Really something -- a God thing I believe. He told me he wanted the tools to go to someone who would use them so that's my mission.
The other good thing is that I was contacted by a man who was wondering if I'd be interested in designing some bar stools for him. Of course I was, we've met and I'm adding this to my list of projects. As luck would have it I decided to take the prototype of the bar stool I designed for my own. It was just about the perfect height, shape, and design and I probably could have sold it right then and there! However, it's made of Poplar with a laminated Walnut back but not finished to the quality I'd let leave the shop, besides, he needs two of them. We made some changes, it'll be made of Hard Maple to match his kitchen cabinets and island and have a laminated back and grid of Chakte Kok (aka Bloodwood). Since two stools are needed I've been busy making the pattern for the legs and improving the lamination form for the back rest. That's the kind of thing that takes an incredible amount of time. It's probably taking 5 times more time to make the form as it will to laminate the backs. There is a possibility of doing a set of chairs for him as well so it's worth it to make a quality form and not toss it like I did with the other.
The first thing I did was to make a pattern out of 1/4" MDF taking time to make the curve as smoothly as possible. The screws used to attach this to a piece of 3/4" MDF will also mark the centers of the holes that will become pockets for the clamps. You can see the plunge router with a bushing that I used to cut 4 pieces. This will be a segmented, male/female form which I've found works the easiest. I'll post more pictures as the work progresses.
Luckily there isn't a huge rush on the bar stools. The TV lift cabinet needs to be completed first and I should be getting the compo for that within the next two days. Once that's all applied I can get it to the faux finisher and concentrate on the other work. What other work? well, besides the stools there are two picture frames I have compo coming for and also a Walnut frame for a painting Diane has entered into a show coming up.
The other good thing is that I was contacted by a man who was wondering if I'd be interested in designing some bar stools for him. Of course I was, we've met and I'm adding this to my list of projects. As luck would have it I decided to take the prototype of the bar stool I designed for my own. It was just about the perfect height, shape, and design and I probably could have sold it right then and there! However, it's made of Poplar with a laminated Walnut back but not finished to the quality I'd let leave the shop, besides, he needs two of them. We made some changes, it'll be made of Hard Maple to match his kitchen cabinets and island and have a laminated back and grid of Chakte Kok (aka Bloodwood). Since two stools are needed I've been busy making the pattern for the legs and improving the lamination form for the back rest. That's the kind of thing that takes an incredible amount of time. It's probably taking 5 times more time to make the form as it will to laminate the backs. There is a possibility of doing a set of chairs for him as well so it's worth it to make a quality form and not toss it like I did with the other.
The first thing I did was to make a pattern out of 1/4" MDF taking time to make the curve as smoothly as possible. The screws used to attach this to a piece of 3/4" MDF will also mark the centers of the holes that will become pockets for the clamps. You can see the plunge router with a bushing that I used to cut 4 pieces. This will be a segmented, male/female form which I've found works the easiest. I'll post more pictures as the work progresses.
Luckily there isn't a huge rush on the bar stools. The TV lift cabinet needs to be completed first and I should be getting the compo for that within the next two days. Once that's all applied I can get it to the faux finisher and concentrate on the other work. What other work? well, besides the stools there are two picture frames I have compo coming for and also a Walnut frame for a painting Diane has entered into a show coming up.
Subscribe to:
Posts (Atom)